Need of Waterproofing
CONCRETE
Contrary to common belief, concrete itself is a complex composite material. It has low strength when loaded in tension and hence it is common practice to reinforce concrete with steel, for improved tensile mechanical properties. Concrete structures such as bridges, buildings, elevated highways, tunnels, parking garages, offshore oil platforms, piers and dam walls all contain reinforcing steel (rebar). The principal cause of degradation of steel reinforced structures is corrosion damage to the rebar embedded in the concrete.
POROSITY IN CONCRETE
When most of us think about concrete, we consider it to be an impenetrable barrier. What most of us don't realize, however, is that concrete is actually a very porous material by nature that will allow moisture to pass through it readily. Or we may call it ‘Hard Sponge’.
Imagine: Average pore size in concrete is 1,000 -10,000 nm where as the diameter of water molecule is only 0.28 nm! The average pore in concrete is at least 3,571.42 times larger than the diameter of a water molecule!
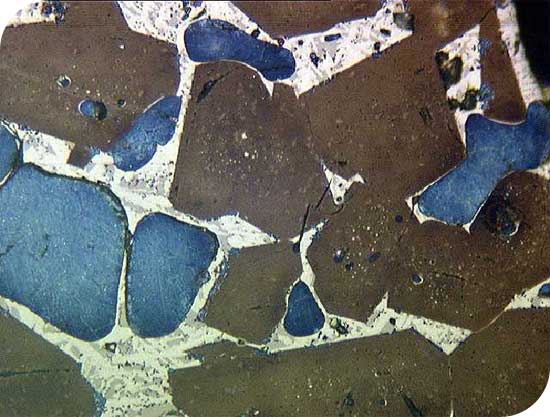
Typical Concrete Structure (Credit: Paul Stutzman, NIST)
Concrete’s porosity has a strong correlation with the water/cement ratio (W/C) but also depends on curing practice, the rheology characteristics of fresh concrete, the mix design etc. It’s not only the pores percentage that counts but also pores sizes, pores distribution and the interconnections between the pores. It’s logical to observe that concrete durability is closely linked to water intrusion and movement rates. Furthermore, water inside concrete’s mass plays the role of the carrier for harmful substances that can potentially have deleterious effects on the concrete and its steel reinforcements.
Water movement inside the concrete has to do with its permeability which is closely related to the total porosity and its distribution in the cementitious matrix of concrete. The building envelope when in contact with water, it absorbs varied degree of amount of water depending on its porosity.
The mechanisms of water uptakes by building materials are as varies as the possible damages it causes to the building.
NEED OF WATERPROOFING
There are many reasons to waterproof concrete. They include health, cost effectiveness, structural integrity, reduced opportunity costs, usage purposes, visual appeal, and to increase the life of a concrete structure.
Here are some of the common problems associated with humidity and moisture ingress;
- Humidity and moisture ingress often result in fungus and mold growth leading to itching, asthma, sneezing and a variety of health related problems.
- Humidity and moisture ruin mortar, paint and drywall and result in costly repairs and unusable spaces.
- Humidity and moisture can lead to the forced closure of hotels, restaurants, bars and impede revenue generation in many businesses.
- Water ingress related problems can lower the value of houses, apartments and businesses.
- Humidity and moisture ingress increase maintenance costs and lower rentability of any structures in which warehousing, housing people or housing animals is necessary.
- Humidity and Moisture can eventually lead to very expensive repairs or even deterioration to the point in which a structure is rendered useless.
While the above listed humidity and moisture problems are commonly understood, what many fail to understand is how the long term costs and problems associated with water ingress into their structures can be prevented through effective waterproofing through crystalline technology.
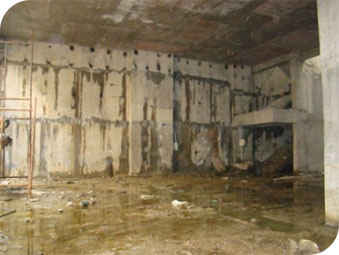
A Leaking Basement
Water ingress is a major contributor to many of the concrete related problems that cause deterioration of concrete within concrete structures. These include corrosion, chlorides, carbonization, alkali-silicate reaction, freeze/thaw, and chemical attack.
Water Ingress and Corrosion
The two most common causes of reinforcement corrosion are (i) localized breakdown of the passive film on the steel by chloride ions and (ii) general breakdown of passivity by neutralization of the concrete, predominantly by reaction with atmospheric carbon dioxide. Sound concrete is an ideal environment for steel but the increased use of deicing salts and the increased concentration of carbon dioxide in modern environments principally due to industrial pollution, has resulted in corrosion of the rebar becoming the primary cause of failure of this material. The scale of this problem has reached alarming proportions in various parts of the world.
Corrosion deterioration in concrete normally occurs due to an electrical reaction caused by exposure of the reinforcing steel to oxygen and moisture. When the iron in the steel oxidizes, it expands, and causes tensile stress in the concrete until eventually the concrete cracks or spalls. As the cracks and spalls begin to occur increased amounts of water and oxygen access the reinforcing steel increasing the rate of corrosion and accelerating the deterioration effects. Stopping water ingress will also stop the effects of corrosion on the reinforcing steel thereby preventing tensile stress cracks and spalling.
Water Ingress and Chlorides
In 1962, it was reported that the required minimum concentration of chloride in the concrete immediately surrounding the steel to initiate corrosion, the chloride corrosion threshold, is 0.15% soluble chloride, by weight of cement. In typical bridge deck concrete with a cement factor of 7, this is equivalent to 0.025% soluble chloride, by weight of concrete, or 0.59 kg soluble chloride per cubic meter of concrete. Subsequent research at FHWA laboratories estimated the corrosion threshold to be 0.033% total chloride, by weight of concrete.
There are indications that the chloride corrosion threshold can vary between concrete in different bridges, depending on the type of cement and mix design used, which can vary the concentrations of tricalcium aluminate (C3A) and hydroxide ion (OH-) in the concrete. In fact, it has been suggested that because of the role that hydroxide ions play in protecting steel from corrosion, it is more appropriate to express corrosion threshold in terms of the ratio of chloride content to hydroxide content, [Cl-] / [OH-], which was recently established to be between 2.5 to 6.
When a concrete structure is often exposed to, salt splashes, salt spray, or seawater, chloride ions from these will slowly penetrate into the concrete, mostly through the pores in the hydrated cement paste. The chloride ions will eventually reach the steel and then accumulate to beyond a certain concentration level, at which the protective film is destroyed and the steel begins to corrode, when oxygen and moisture are present in the steel-concrete interface. Even high alkalinity will have minimal abilities to reduce deterioration. If water ingress is stopped even cast in chlorides will not deteriorate the concrete.
Water Ingress and Carbonization
Corrosion can also occur even in the absence of chloride ions. Carbonization is a chemical reaction between carbon dioxide in the air and the calcium hydroxide in the hydrated cement paste and with the presence of moisture reduces the pH of the concrete through the creation of carbonic acid. Over time this process will lower the pH as low as 8.5 of the concrete thereby permitting corrosion of the embedded steel. By stopping water ingress the effects of carbonization can be dramatically reduced.
Water Ingress and Alkali-Silica Reaction/ Alkali Aggregate Reaction
ASR (Alkaline Silica Reaction) or AAR (Alkaline Aggregate Reaction) are basically a reaction that occurs when alkaline contaminated aggregates and moisture ingress cause an expanding gel to form around the cast in aggregates in the concrete. The expansion of the aggregates causes cracking and spalling of the concrete and the entry of more moisture ingress. Stopping water ingress can stop the expansion process of the silicate reaction formed around the gel and prevent expansion of the gel formed around the aggregate thereby preventing cracking and spalling.
Multiguard In-depth Crystalline waterproofing is a very interesting and promising concept and it will surely draw more and more attention in the future as the relevant technology makes leaps.
|